Leveling Machines Explained: How They Work, What's Inside, Where They're Used & What's Next
How Leveling Machines Work
Leveling machines fix wavy bends, curves, and twists in metal sheets or coils. These defects often happen during rolling, cutting, or transport. The machine works by applying pressure and bending force to the metal. This redistributes the internal stresses within the metal.
The core part is a set of rolls stacked above and below the metal. As the sheet or strip passes through these rolls, it gets bent back and forth multiple times. This bending exceeds the metal's yield strength (meaning it starts to bend permanently). This process releases and rebalances the internal stresses, leaving you with a much flatter, straighter piece of metal.
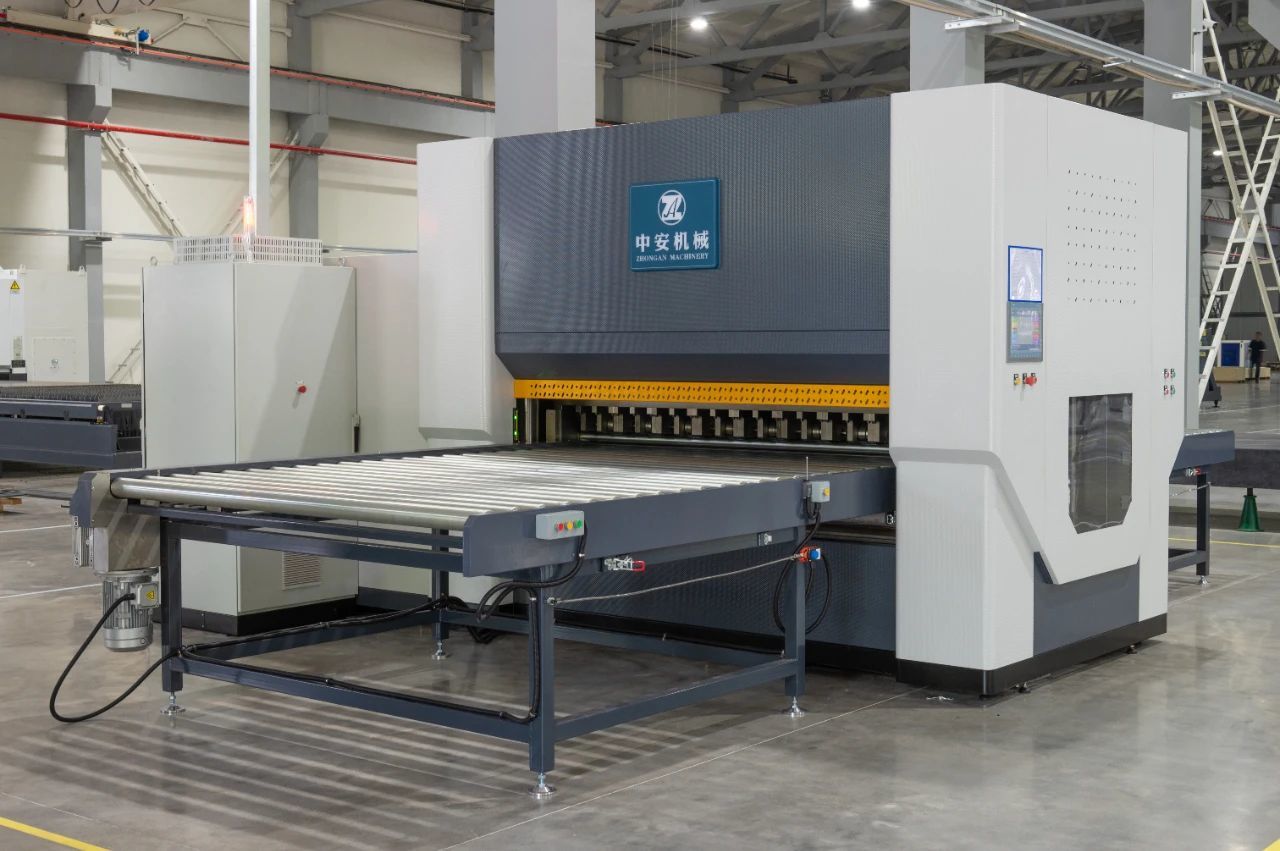
What Makes Up a Leveling Machine?
The Roll Assembly: The heart of the machine. These rolls are usually made from high-grade alloy steel or tool steel. They're hardened, ground, and polished for maximum hardness and wear resistance. The gap between the top and bottom rolls can be adjusted for different metal thicknesses and flatness requirements.
The Drive System: Powers the rolls to rotate and pull the metal through. It typically includes motors, gearboxes, and couplings. This system provides the necessary speed and torque.
The Support System: Holds everything rigidly in place and handles the massive forces generated during leveling. It includes a sturdy frame (often heavy cast iron or welded steel), bearing blocks, and tie rods to ensure stability and precision.
The Control System: Manages the machine's operation – roll speed, gap settings, pressure, etc. – for precise results on different materials. Modern controls use PLCs and touchscreens, making them easy to operate, highly accurate, and very reliable.
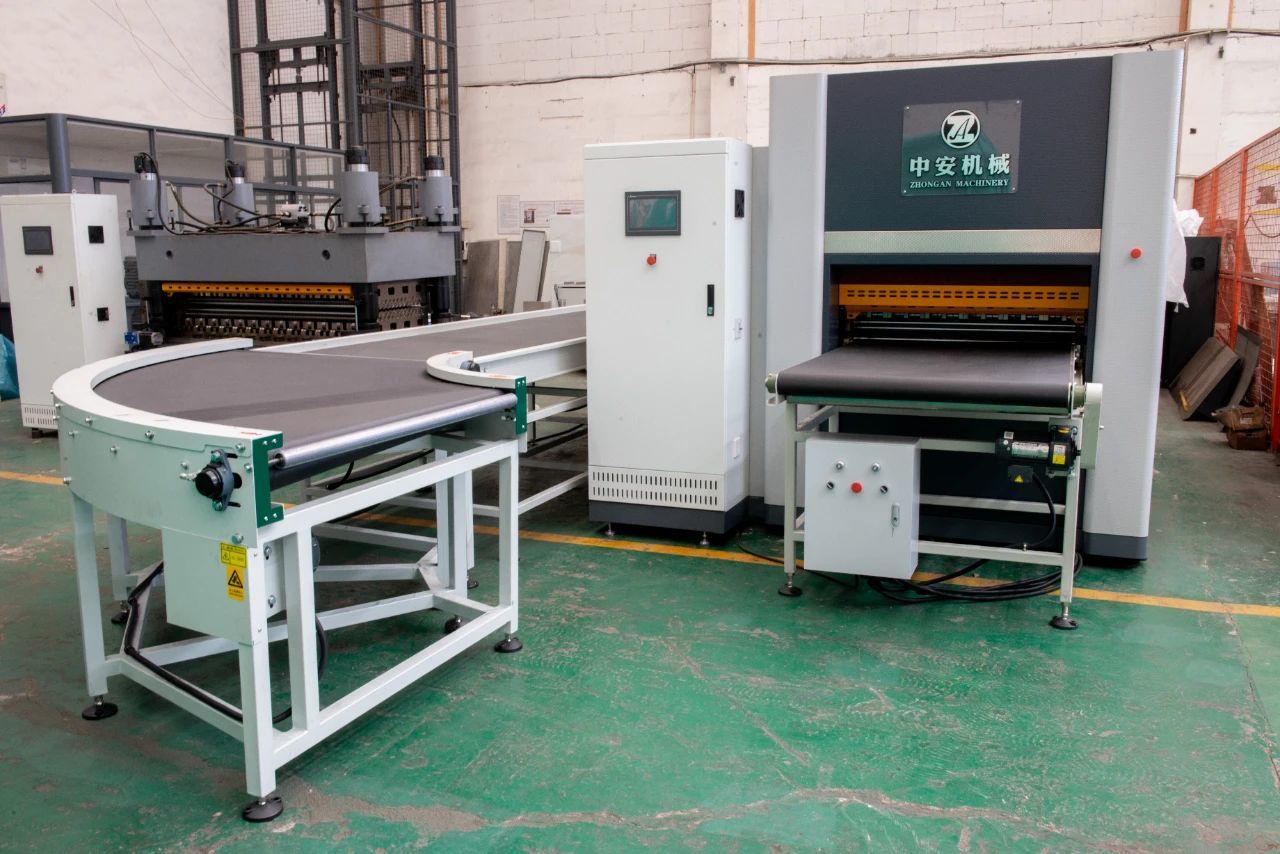
Where Are Leveling Machines Used?
Automotive: Essential for preparing body panels (like doors, hoods, trunk lids), chassis parts, and engine covers. Leveling ensures these parts are flat and dimensionally accurate for better quality and easier assembly.
Aerospace: Demands extreme flatness and precision. Leveling is crucial for making aircraft wings, fuselage skins, and engine components meet strict aerospace standards.
Construction: Used on metal panels like painted steel (cladding) or aluminum (for curtain walls). Leveling gives panels a smooth, attractive finish and improves performance (like weather resistance).
General Machinery Manufacturing: Needed for parts like machine housings, work tables, and guide rails. Leveling ensures these components are flat, leading to better overall machine quality and performance.
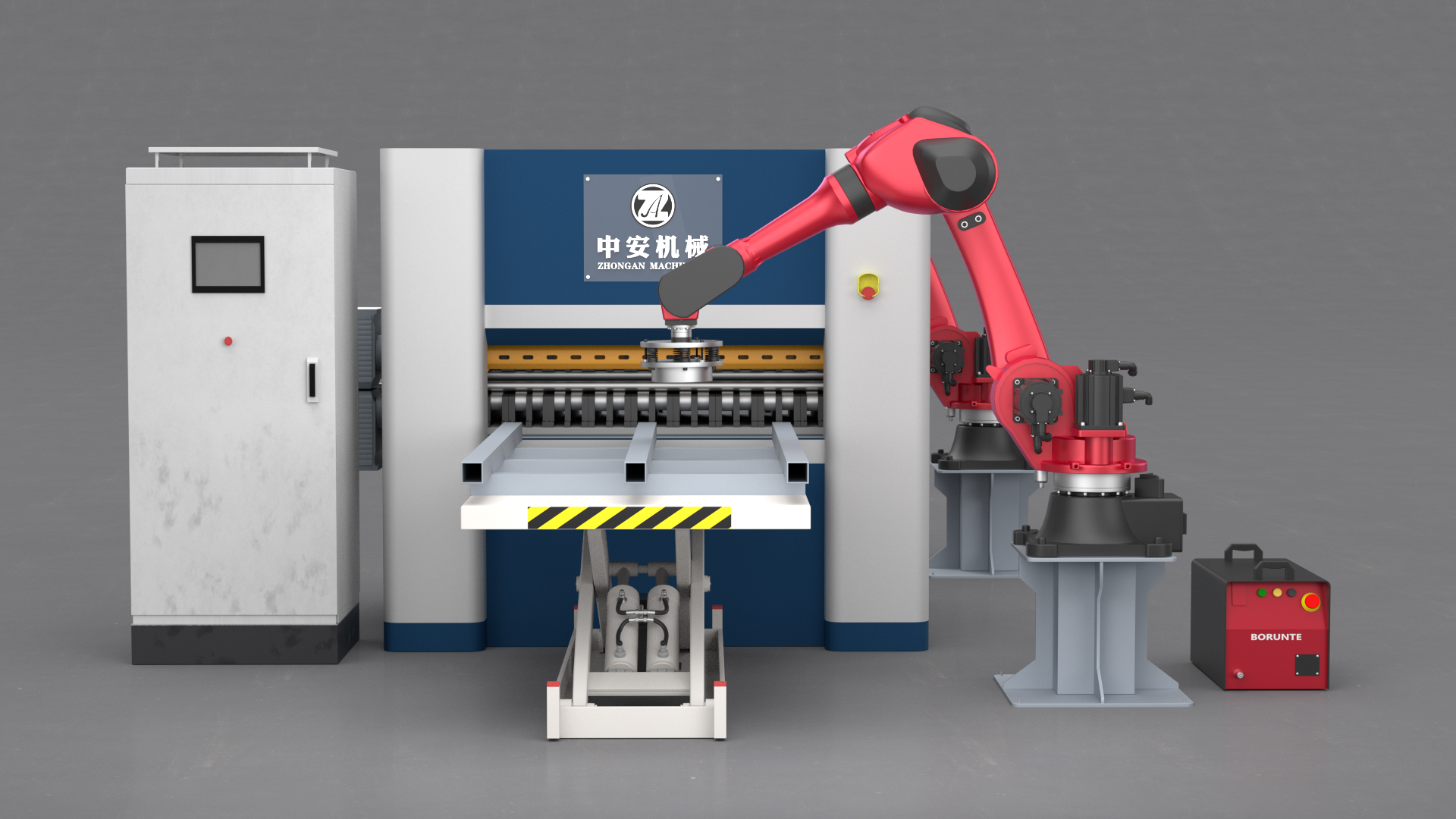
What's Next for Leveling Technology?
Higher Precision: As industries demand ever-flatter metal, leveling machines are getting more precise. Expect better manufacturing techniques and smarter controls pushing accuracy even further.
More Automation & Intelligence: Machines are getting smarter to boost efficiency and reduce manual work. Sensors and AI-powered controls will monitor flatness in real-time, automatically adjust settings, and could even run with minimal human oversight.
Combined Functions (All-in-One Lines): To streamline production, levelers will increasingly be integrated with other machines. Think combined lines that level, then cut, shear, or punch the metal – all in one continuous flow. This saves space and time.
Energy Efficiency & Eco-Friendliness: Driven by sustainability goals, new machines will focus on using less power (efficient motors/drives) and reducing environmental impact (less noise, less dust).
Related News
undefined